Order Picking
What Is Order Picking?
Order picking is a critical process in warehousing and fulfillment, where products or SKUs (stock-keeping units) are selected to fulfill customer orders. As the first step in order fulfillment, efficient order picking plays a critical role for businesses to deliver orders accurately and quickly, streamlining the remaining steps in the order fulfillment process — packing, shipping, and delivery down to the last mile.
With the rise of omnichannel fulfillment, order picking takes place across several different areas of a business, from warehouses and distribution centers to brick-and-mortar retail stores fulfilling orders for in-store pickup. Implementing the right order picking solutions — like warehouse storage systems and tailored order picking strategies — enables businesses to boost productivity and order accuracy, enhance storage density, and lower labor costs through efficient operations.
Common Types Of Order Picking
The right order picking method depends on your warehouse layout, inventory, and order volume. Here are the most common types:
- Single order picking or discrete order picking enables pickers to focus on one item at a time. This basic order picking style is ideal for smaller operations with fewer SKUs.
- Batch picking, also referred to as multi-order picking, involves groups of orders simultaneously, which is helpful for small items or orders with minimal SKUs. This type of picking reduces the amount of time needed to process SKUs.
- Wave picking is where one worker picks one order, one SKU at a time, but orders are scheduled to be picked at certain times in a specific wave to maximize picking and packing operations. This method is very efficient when large numbers of SKUs are picked because it significantly reduces travel time.
- Zone picking reduces travel time by assigning pickers to one specific warehouse zone to pick within, filling orders with the SKUs in that area.
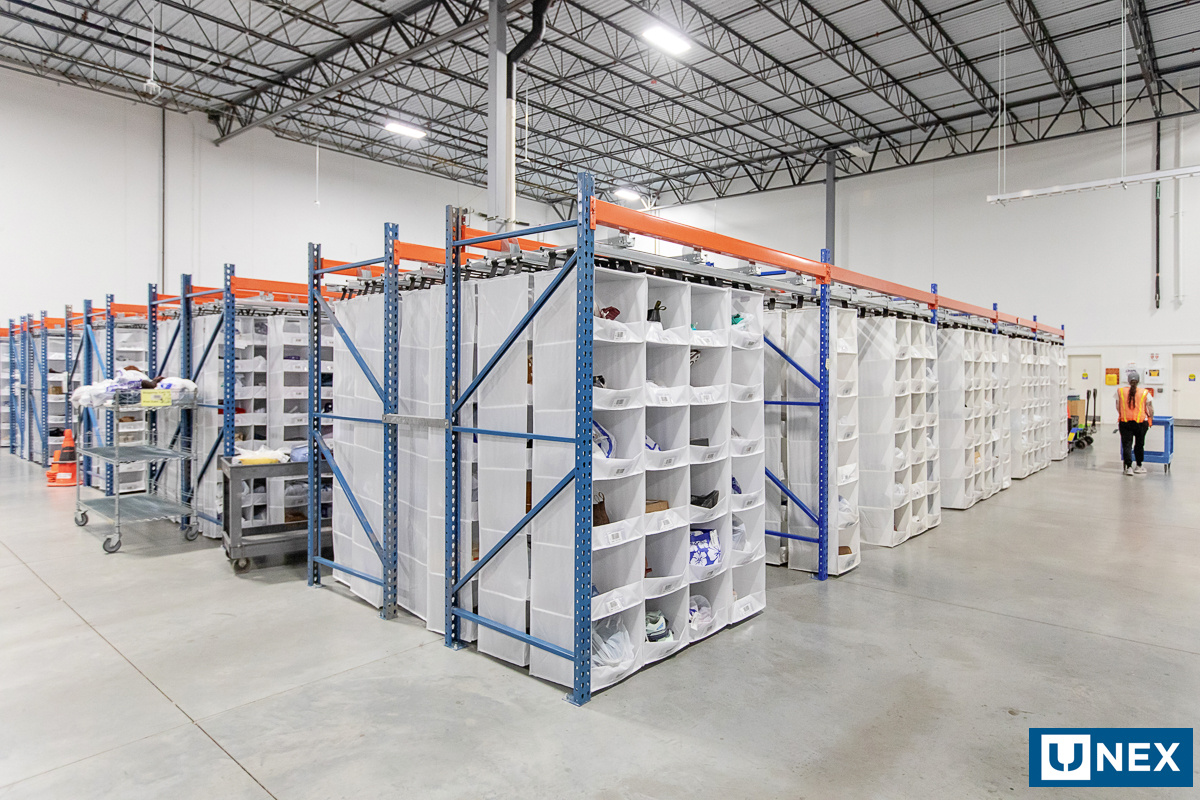
Order Picking Challenges
While order picking is vital within the order fulfillment process, it is often prone to several errors. The average industry picking error rate is between 1% and 3%. While seemingly minor, this can add up to $50 to $300 cost per error. Common order picking challenges include:
- SKUs placed in incorrect locations or inefficiently organized
- Lack of organization by throughput, resulting in delayed or missed orders
- Hiring qualified pickers or inability to train pickers on warehouse layout and item locations
- Inefficient use of picker time due to warehouse layout and storage system
Ready to Connect with an Expert?
Fill out the form below to request a consultation to find the ideal order picking solutions for your unique space.
Best Practices to Improve Order Picking
Following order picking best practices will ultimately improve customer service, boost worker productivity, reduce costs, and increase the overall bottom line.
- Create “hot zones” for fastest moving SKUs to reduce travel distance and picking time. Place in highly accessible carton flow racks or high-density storage solutions.
- Have discrete pick locations so pickers don't have to search through items, improving speed.
- Utilize conveyors and sorters to bring ordered items to pickers to decrease walking time.
These are a few simple steps businesses can take to ensure order picking operations are running at peak efficiency and improving outcomes, including reduced labor costs, faster fulfillment, lower picking errors, and improved warehouse productivity.
Improve Order Picking Speed and Reduce Labor Costs
On their own, pallet racks help to maximize the use of limited space and organize picks throughout a warehouse. To realize the full potential of warehouse pallet rack storage systems and improve order picking procedures, implement rack enhancements such as UNEX SpeedCell, SpanTrack, Shelf Track, and Pallet Track. A trusted industry provider of robust, made-to-order storage solutions, UNEX products condense storage space to improve SKU layout and reduce pick times which, in turn, reduces labor costs.
These dynamic storage solutions streamline order picking processes to reduce labor costs by up to 40%, improve inventory accuracy, and support strong warehouse efficiency.
Increase Storage Density and Improve Picking Processes
Long travel times in a warehouse reduce the number of orders processed daily. UNEX order picking solutions, such as SpanTrack and SpeedCell, maximize storage density by minimizing wasted space. These systems support faster order picking operations, ensuring high throughput and accurate fulfillment.
Optimize Your Order Picking Operations with UNEX
UNEX order picking solutions are easy to integrate into existing rack structures and designed to help you get the most out of your warehouse space, distribution center, or retail backroom. UNEX solutions are ideal for order fulfillment, logistics, and retail operations looking to increase storage density and improve order picking processes.
Connect with our product experts to learn how UNEX solutions can help you increase space utilization and streamline your order picking processes.
Explore UNEX Solutions
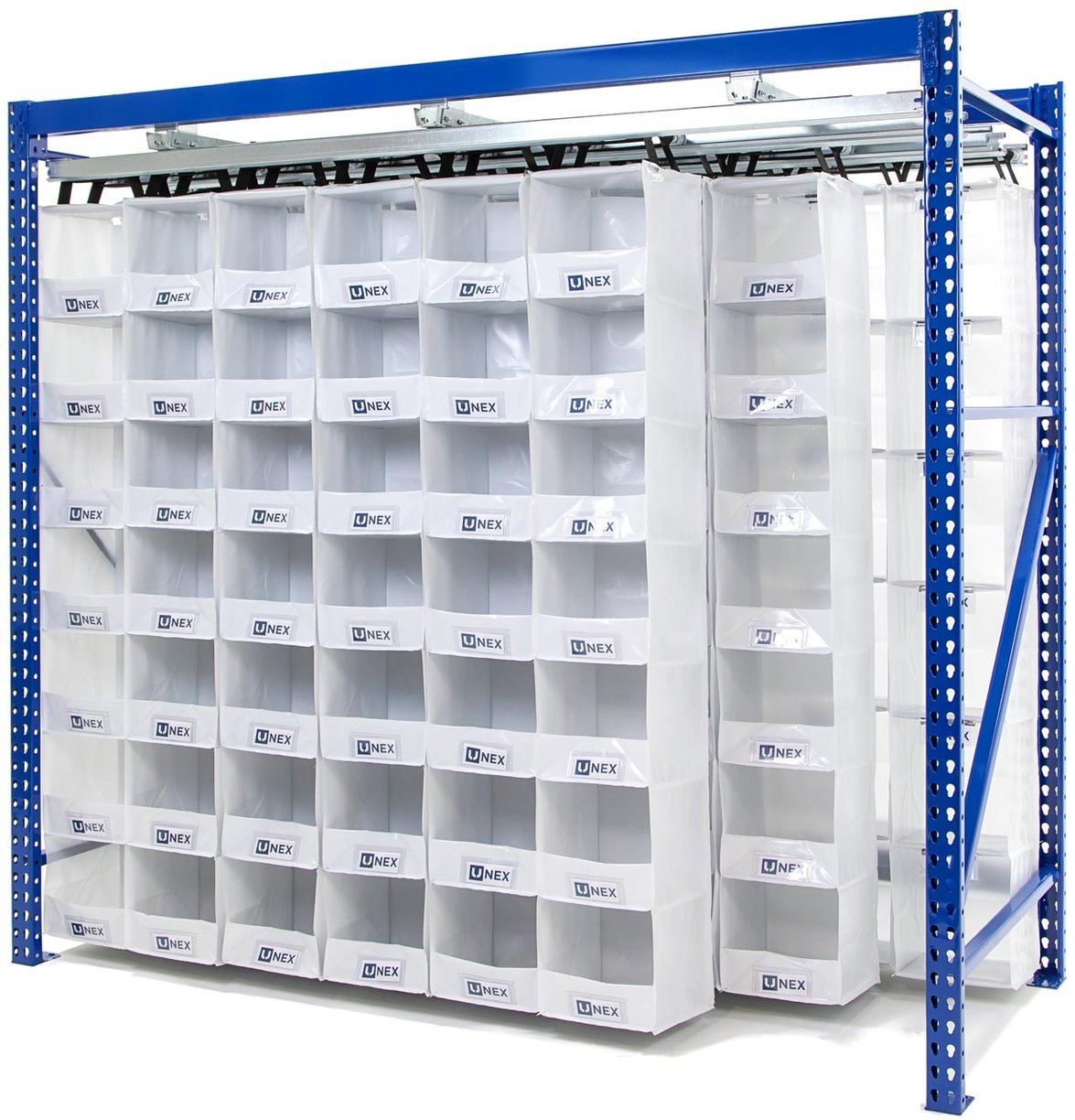
SpeedCell
SpeedCell is a dynamic warehouse storage solution uniquely designed to save time, space, and money by using existing space within standard pallet racking. Its compact design can compress 200′ of rack or shelving into 40′ of highly organized space.
Key benefits of SpeedCell include:
- Transform vacant space into useable storage and increase storage density by 40-60%
- Create a highly efficient and accurate pick
- Reduce picker travel time by 80%
- Reduce labor costs by up to 40%
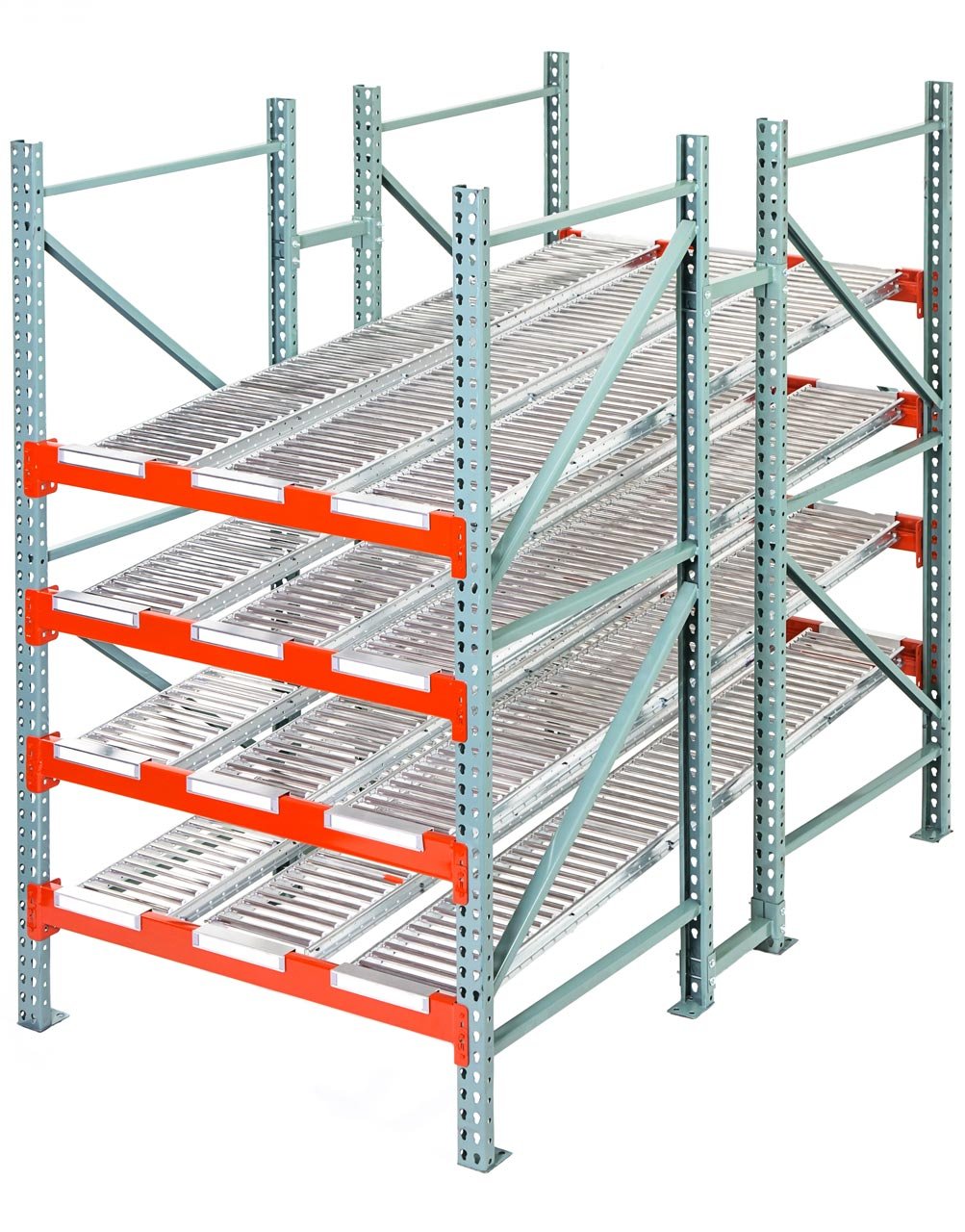
SpanTrack Lane
SpanTrack Lane is an innovative carton-flow solution that drops into new or existing pallet rack structures to create an efficient, reliable, and durable flow system. Depend on a robust and sturdy solution for even the most active warehouses and assembly plants.
Key benefits of Spantrack include:
- Ensure FIFO inventory rotation
- Reduce worker travel time by up to 75%
- Optimized for product stacking
- Industry-leading 7-year warranty
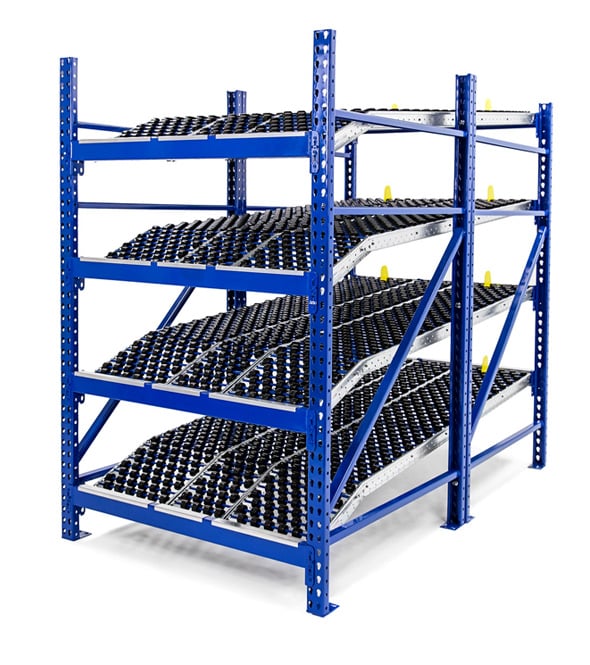
SpanTrack Wheel Bed
SpanTrack Wheel Bed is a flexible carton flow solution that drops into new or existing pallet rack structures to create the ultimate gravity flow rack system for order picking operations, manufacturing facilities, and more.
Additional Benefits Of Spantrack Wheel Bed Include:
- Hex hub wheel design for optimal flow
- Store products with a wide variation in size and weight
- Increase flexibility for inventory slotting with 90% left to right bay usage
- Replenish inventory from the back without interrupting the process in front
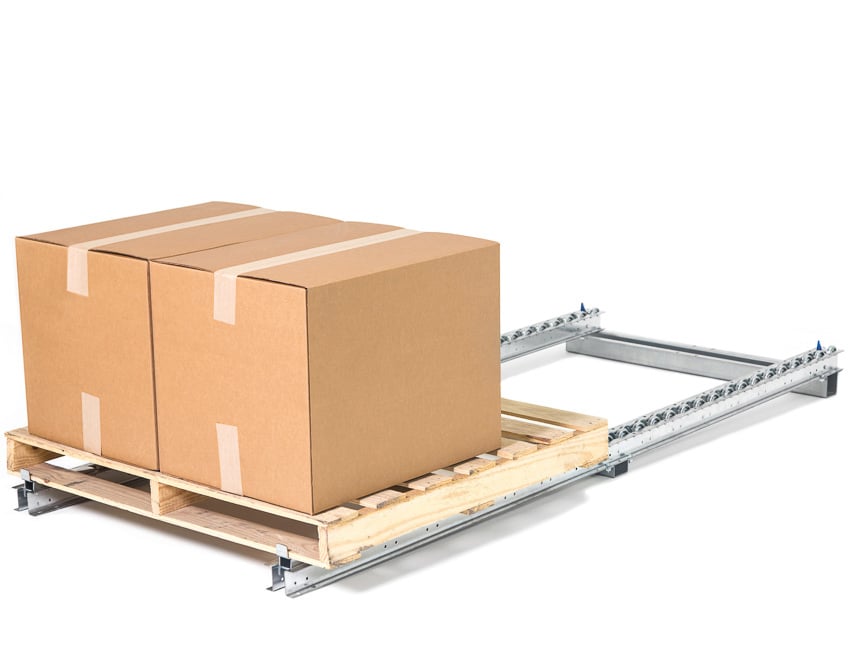
Pallet Track
Pallet Track is a durable pallet flow solution that utilizes rollers or wheel rails to optimize flow for fast-moving inventory. Our high-quality pallet tracks increase efficiency and storage density and can be customized to fit an operation’s unique needs.
Key benefits of Pallet Track include:
- Select from a variety of track lengths and mounting options
- Increase storage density
- Reduce fork truck operations
- Decrease damage to inventory
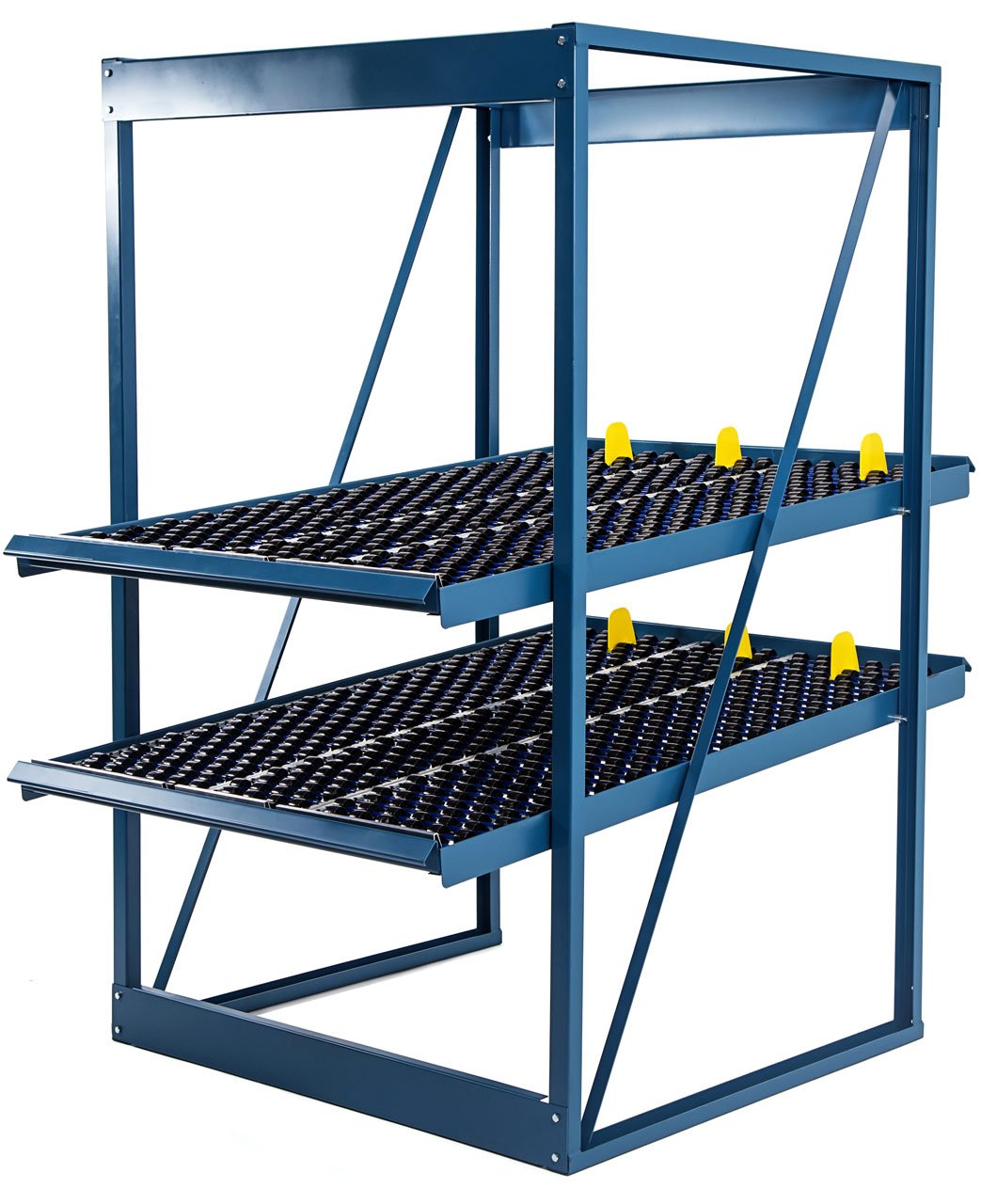
Shelf Track
Shelf Track is a carton flow system that replaces unreliable plastic wheel rails and integrates easily into existing racks and shelves. The drop-in design helps create an efficient and accessible pick point for workers and increases productivity.
Key benefits of Shelf Track include:
- 300% more surface area compared to plastic wheel rails
- Works with almost any shelf and accessories
- Minimize maintenance and replacement costs
- Achieve unrivaled flow
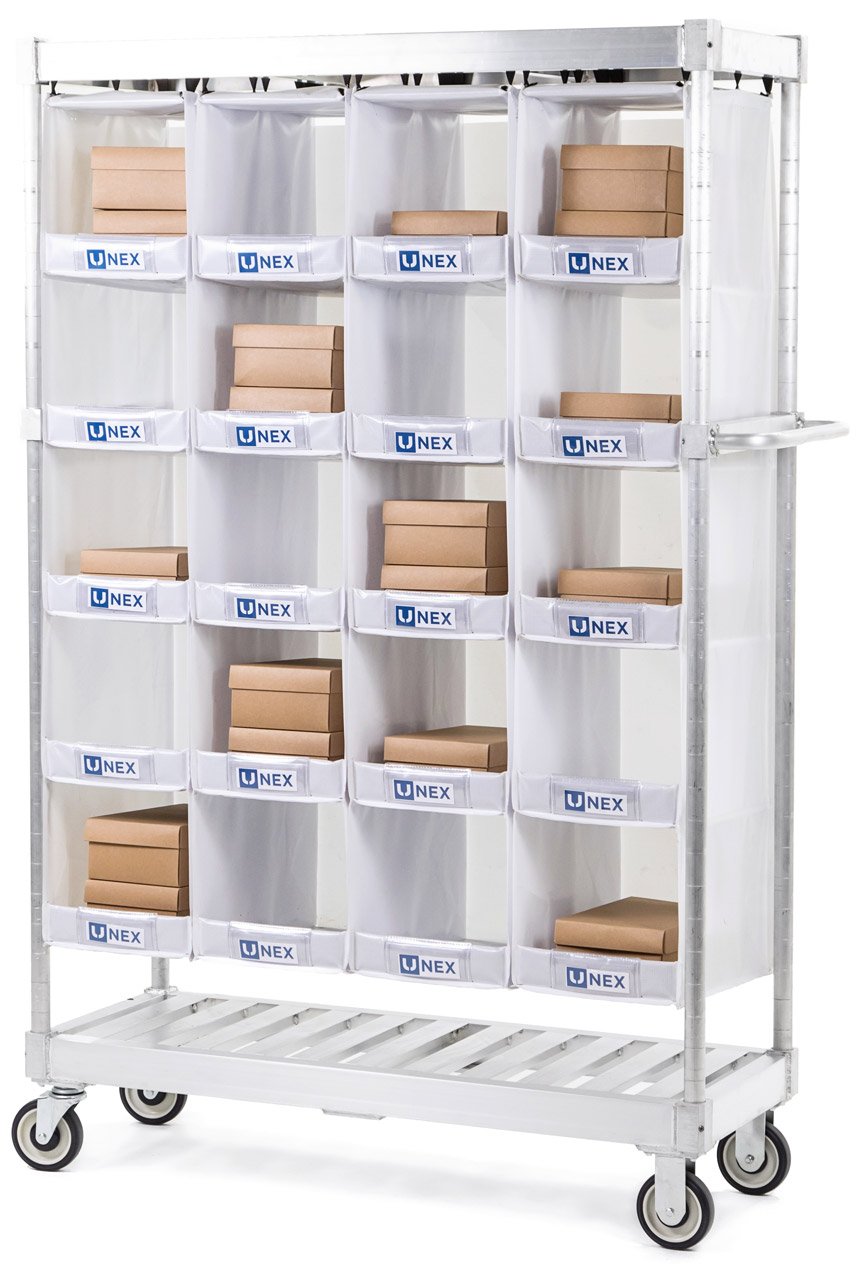
SpeedCartt
SpeedCartt is a mobile, high-density picking cart solution that is reliable in the most demanding environments. Constructed from the same lightweight yet heavy-duty materials as SpeedCell, SpeedCartt improves efficiency and reduces labor costs.
Additional Benefits Of SpeedCartt Include:
- Increase pick facings
- Reduce travel times
- Increase order accuracy
- Pick multiple orders at the same time for maximum efficiency
More Applications
Connect with an Expert
Get in touch with our team of experts to learn how our order picking solutions help maximize space utilization.